The structure of a stacker forklifts. The electric pallet stacker mainly consists of gantry electrical, oil pump box, control handle, driving wheel, balance wheel, etc. Electric forklift manufacturers often integrate the driving wheel and steering wheel of the electric pallet stacker as a whole, that is, the driving wheel also serves as the steering wheel. The electric motor is arranged vertically, and the brake is installed on the upper shaft end of the electric motor.
The control handle of the electric pallet handling and stacking truck has three cams, one of which controls the reverse switch and the other two control the forward gear switch.
Whether manual or stacker forklifts, there is a pair of dynamic balancing wheels on both sides of the driving wheels; There is an eccentricity between the balance wheel frame axle and the wheel axle to ensure follow-up performance; The dynamic balancing wheel is often equipped with compression springs to adapt to uneven road surfaces, ensuring sufficient adhesion quality of the driving wheel.
Performance parameters of the stacker truck. The performance parameters of stacker forklifts mainly include rated lifting weight, load center distance, maximum lifting height, leg insertion height, minimum turning radius, etc.
The stability of electric forklift manufacturers' vehicles refers to their ability to resist tilting under various working conditions, which needs to be estimated in the overall design. After the sample vehicle is manufactured, it needs to be placed on an overturning platform for experimental verification. The platform inclination index is the stability index of the vehicle. It is the ratio of the distance between the vehicle's comprehensive center of gravity at the horizontal projection point and the overturning axis of the vehicle under this working condition to the height of the vehicle's comprehensive center of gravity.
When designing a stacker forklift, a mathematical model can be established according to the requirements of the tilting platform test for estimation. The mathematical model needs to consider factors such as vehicle manufacturing and assembly errors, elastic deformation of the gantry and tires, and imprecise setting of the overturning axis. The simplified mathematical model estimates for the rigidity assumption of electric forklift manufacturers are often lower than the actual platform inclination in experiments.
-
Breakthrough improvements in bucket tines and masts"
Four-wheel drive off-road forklift installation bucket price shovel forklift truck with two vehicles
...Do you like ?0
Read more -
New energy forklift power system controller
The origins of forklifts can be traced back to 1917. After more than 100 years of development, forklifts, as the main mechanized loading and unloading, stacking and short-distance transportation tools, liberate people from heavy primitive human handling. Forklifts are widely used in factories, warehouses,...
Do you like ?0
Read more -
Electric forklifts vs. internal combustion forklifts
An electric forklift is a forklift that is powered by electric energy, usually using a battery as an energy source. A battery is a type of battery that is able to store a limited amount of electrical energy and release it when needed.
Do you like ?0
Read moreWhat are the daily maintenance of electric forklifts?
Electric forklifts are important equipment in warehousing...Do you like ?0
Read more"Electric Forklift Maintenance: Longer Life and More Efficiency"In view of the fact that many friends are still confused about the maintenance of electric forklifts, Xiaobian specially summarized the maintenance knowledge of electric forklifts<...
Do you like ?0
Read more"Level 3 maintenance is indispensable! Forklift maintenance strategy"First, the key points of the first-level maintenance of forklifts
...Do you like ?0
Read more
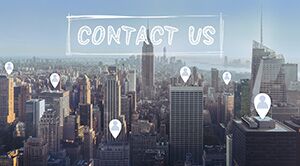
Technical Support: Magic Lamp