What should I do if the forklift cylinder leaks? This one will help you out!
Forklift hydraulic system fault diagnosis and maintenance: in-depth analysis of cylinder problems
The hydraulic system of the forklift is the key to the normal operation of the forklift, and the failure of the cylinder, as one of the core components of the hydraulic system, will directly affect the lifting, lowering and tilting functions of the forklift. This article will deeply analyze the common oil leakage problems and maintenance methods of forklift cylinders, and take manual forklifts as an example to analyze the troubleshooting steps of cylinder faults in detail.
1. Forklift cylinder leakage: phenomenon, causes and solutions
1. Endoleakage
Oil cylinder leakage is one of the common faults of forklifts, which can lead to problems such as weak lifting of forklifts, sliding forks, and forward tilting of masts.
2. Oil leakage from the valve body
2. Troubleshooting steps for manual forklift cylinders
When the following phenomena occur in a manual forklift, it indicates that there may be a problem with the cylinder:
Manual forklift cylinder troubleshooting steps:
3. Precautionary measures
Through the above steps and methods, I believe you have a deeper understanding of the diagnosis and troubleshooting of manual forklift cylinder faults.
Regularly inspect and maintain the hydraulic system of the forklift, and replace aging or damaged seals in a timely manner.
Use hydraulic fluids that meet standards and change them regularly.
Operate the manual forklift correctly to avoid overloading or improper operation causing impact on the hydraulic system.
After loading, the pressure is automatically relieved, and the fork cannot be lifted.
Cylinder leakage.
Manual forklift forks are completely incapable of lifting.
Manual forklift forks descend slowly or fail to descend.
Phenomenon: Oil stains appear on the outside of the valve body.
Common causes: Aging or damage to the O-ring seal between stem and body.
Solution: Replace the O-ring.
For worn bodies, chrome polishing or replacement can be selected depending on the degree of wear.
Replace aged, damaged seals and inspect the valve body for damage to ensure proper installation.
Replace the failed safety valve spring.
Check the multi-way reversing valve, repair or replace the deformed or damaged return spring, clean the inside of the valve body, and eliminate jamming.
Grind or replace worn poppet valves.
Valve body wear: Long-term use of the distribution valve or oil contamination leads to wear of the valve stem and valve body, damage to the sealing surface, and internal leakage.
Seal failure: Weathering, damaged, or improperly installed seals cause oil to leak inside the valve body.
Safety Valve Failure: The safety valve spring fails, and the hydraulic oil flows into the spill tract below the set pressure, causing internal leakage.
Multi-way directional valve failure: The valve stem cannot be reset, resulting in collusion of the oil circuit and internal leakage.
Cone valve wear: Cone valve wear leads to poor oil channel closing, hydraulic oil backflow, and system failure.
Phenomenon: The manual forklift is slow and weak, the fork slides down by itself, and the mast leans forward by itself.
Common causes:
Solution:
Check the cylinder seals: The cylinder seals of manual forklifts are mainly distributed in the contact parts between the piston rod and the cylinder, the bottom of the cylinder block and the oil injection port. Inspect the seals for age, damage or deformation.
Replace the seal: Use
-
Breakthrough improvements in bucket tines and masts"
Four-wheel drive off-road forklift installation bucket price shovel forklift truck with two vehicles
...Do you like ?0
Read more -
New energy forklift power system controller
The origins of forklifts can be traced back to 1917. After more than 100 years of development, forklifts, as the main mechanized loading and unloading, stacking and short-distance transportation tools, liberate people from heavy primitive human handling. Forklifts are widely used in factories, warehouses,...
Do you like ?0
Read more -
Electric forklifts vs. internal combustion forklifts
An electric forklift is a forklift that is powered by electric energy, usually using a battery as an energy source. A battery is a type of battery that is able to store a limited amount of electrical energy and release it when needed.
Do you like ?0
Read moreWhat are the daily maintenance of electric forklifts?
Electric forklifts are important equipment in warehousing...Do you like ?0
Read more"Electric Forklift Maintenance: Longer Life and More Efficiency"In view of the fact that many friends are still confused about the maintenance of electric forklifts, Xiaobian specially summarized the maintenance knowledge of electric forklifts<...
Do you like ?0
Read more"Level 3 maintenance is indispensable! Forklift maintenance strategy"First, the key points of the first-level maintenance of forklifts
...Do you like ?0
Read more
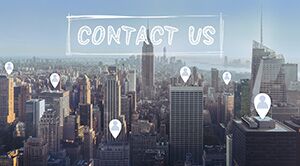
Technical Support: Magic Lamp