Electric forklift controller circuit diagram, how much do you know?
Circuit diagram analysis of electric forklift controller
This article will analyze the circuit diagram of the electric forklift controller in detail, and analyze its working principle and debugging method in combination with the actual application scenarios.
Circuit principle
1. Power Circuit:
The controller adopts a regulated power supply circuit to convert the 36V voltage of the battery into 12V to supply power to the control circuit. The regulated power supply consists of TL431 and Q3, and the 12V supply voltage can be calibrated by adjusting the VR6.
2. PWM Generation Circuit:
The PWM circuit uses the TL494 pulse-width modulator as the core, and generates an oscillation frequency of about 12kHz through R3, C4, and the internal circuit.
3. Motor drive circuit:
The motor drive circuit is composed of Q1, Q2, Q4 and other components to control the permanent magnet DC brush motor. The width-shifting pulse output by TL494 is reversed-phase amplified by Q1 to drive VDMOS transistor Q2. The wider the low-level part of the widened pulse output of the (8) pin of the TL494, the longer the Q2 on-time and the higher the motor speed. D1 is the motor freewheeling diode to prevent Q2 breakdown.
4. Battery discharge indication circuit:
The discharge indication circuit uses LM324 chip, through four comparators, according to the change of battery voltage, to control the LED light to indicate the battery power status.
5. Battery over-discharge protection circuit:
When the battery voltage is lower than 31.5V, the (1) pin of LM324 outputs a low level, and the triode Q5 is turned on, forcing the TL494 to cut off the internal widening pulse output tube, and the motor stops running and enters the battery protection state.
6. Motor over-current protection circuit:
When the motor current exceeds the set value, the sampling voltage on the R30 exceeds the threshold, and the TL494 internal op amp 2 outputs a high level to stop the motor from running and protect the motor.
7. Brake Protection:
When braking, KEY2 is turned on, forcing the TL494 to cut off the internal widening pulse output tube, and the motor stops running.
debugging
During the debugging process, the speed regulation circuit, braking circuit, overcurrent protection circuit, and battery discharge indication circuit should be tested respectively to ensure the normal operation of each functional module.
Fuel level display circuit
The fuel display circuit uses the LM339 chip, which controls the LED light to turn on and off according to the change of battery voltage to indicate the battery level.
Improvement scenarios
Application scenarios
The circuit diagram of the electric forklift controller is widely used in various electric forklifts to control the speed, direction, braking and other functions of the motor to improve work efficiency and safety.
summary
This article analyzes the circuit diagram of the electric forklift controller in detail, and introduces its working principle, debugging methods and application scenarios. We hope to help readers better understand the design and application of electric forklift controllers.
Use Hall speed knob instead of photoelectric speed knob.
Use a microcontroller for more complex control functions
-
Breakthrough improvements in bucket tines and masts"
Four-wheel drive off-road forklift installation bucket price shovel forklift truck with two vehicles
... -
New energy forklift power system controller
The origins of forklifts can be traced back to 1917. After more than 100 years of development, forklifts, as the main mechanized loading and unloading, stacking and short-distance transportation tools, liberate people from heavy primitive human handling. Forklifts are widely used in factories, warehouses,...
-
Electric forklifts vs. internal combustion forklifts
An electric forklift is a forklift that is powered by electric energy, usually using a battery as an energy source. A battery is a type of battery that is able to store a limited amount of electrical energy and release it when needed.
Do you like ?189
Read more -
What are the daily maintenance of electric forklifts?
Electric forklifts are important equipment in warehousing...Do you like ?151
Read more -
"Electric Forklift Maintenance: Longer Life and More Efficiency"
In view of the fact that many friends are still confused about the maintenance of electric forklifts, Xiaobian specially summarized the maintenance knowledge of electric forklifts<...
-
"Level 3 maintenance is indispensable! Forklift maintenance strategy"
Do you like ?135
Read more
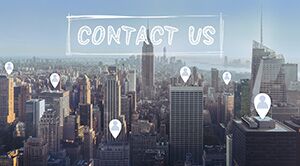