The first level maintenance of electric forklifts and tractors mainly focuses on visual inspection and external clearance adjustment, as we have already discussed before. The second level maintenance mainly focuses on internal adjustment of components, elimination of defective conditions, and local repair and replacement of parts. The following are the details of secondary maintenance:
(1) Secondary maintenance of electric forklifts
The secondary maintenance content of electric forklifts is as follows:
1. Complete the first level maintenance regulations and meet the technical requirements;
2. Check the gantry, fork, guide wheels, and lateral guide wheels of the gantry mechanism and adjust the clearance; Check the chain and adjust it; Check for cracks, open welds, and deformations in the gantry and fork frames, and clean all components;
3. Check the hydraulic system. Disassemble and inspect the oil pump: When the oil pump is weak, noisy, or overheated, it should be disassembled and inspected to eliminate the fault. Disassemble and inspect the oil cylinder: When the oil cylinder is weak or has severe oil leakage, the oil cylinder should be disassembled and replaced with a failed oil seal, and the cylinder body, piston rod lowering speed limit valve, and other components should be inspected and troubleshooting should be eliminated. Disassemble and inspect the multi way directional valve: When there is serious leakage or abnormal operation, it should be disassembled and inspected to eliminate the fault and adjust the pressure value. Clean the oil tank, replace the hydraulic oil, remove the oil outlet filter, and inspect the hydraulic oil pipe;
4. Check and adjust the drive axle of the electric forklift. Disassemble and inspect the gearbox and internal diagonal wheel set, and check the wear and engagement status of the main and passive cone wheel sets; Check the alignment between the planetary gear and the half shaft gear; Check the half shaft and housing, and replace the wheel oil; Check the wheel bearings and tires;
5. Check the braking system. Check the wheel brakes, disassemble the brake master, and inspect the brake oil pipes and joints; Check the handbrake;
6. Check the steering axle and steering system. Check the wheel bearings and tires; Disassemble and inspect the steering knuckle shaft and steering beam crossbeam; Disassemble and inspect the sector plate and central shaft; Disassemble and inspect the longitudinal and transverse tie rods; Disassemble and inspect the steering gear, inspect and adjust various parts of the components;
7. Check the electrical system. Disassemble and inspect the running motor, oil pump motor, and steering oil pump motor; Disassembly and inspection
Speed controller, switches, and electrical control board; Check the battery box; 8. Check the vehicle body and others. Check for cracks, open welds, and deformations in metal structural components and repair them; Check seat connections and foreskin; Check the connection of counterweights and other components; Paint the entire vehicle, repaint the logo and vehicle number; 9. Test run inspection and acceptance: Check various performance under no-load and heavy-duty conditions. For places with conditions, the electric forklift oil pump and multi way directional valve can be disassembled and inspected. If conditions permit, it is strictly prohibited to disassemble the oil pump and multi way directional valve.
(2) Secondary maintenance of electric traction vehicles
The secondary maintenance content for electric traction vehicles is as follows:
1. Complete all the contents of the first level maintenance;
2. Disassemble, inspect, and clean the interior of the motor, measure the insulation resistance of the armature winding and the excitation winding (when measured with a megohmmeter, the insulation resistance between the electric winding and the excitation winding and the casing should not be less than 1 megohm); Clean and refurbish the commutator and carbon brush;
3. Check whether the silicon controlled rectifier, plug-in board socket and 19 core plug of the governor are damaged, and whether the sector bakelite wheel of the commander and the pinion of the Potentiometer are slipping or disengaged;
4. Disassemble, clean and adjust the brake and steering devices;
5. Check the connectors and contacts of each contactor of the electric traction vehicle for poor contact and damage; Tighten all wiring screws;
6. Check each battery casing
-
Breakthrough improvements in bucket tines and masts"
Four-wheel drive off-road forklift installation bucket price shovel forklift truck with two vehicles
... -
New energy forklift power system controller
The origins of forklifts can be traced back to 1917. After more than 100 years of development, forklifts, as the main mechanized loading and unloading, stacking and short-distance transportation tools, liberate people from heavy primitive human handling. Forklifts are widely used in factories, warehouses,...
-
Electric forklifts vs. internal combustion forklifts
An electric forklift is a forklift that is powered by electric energy, usually using a battery as an energy source. A battery is a type of battery that is able to store a limited amount of electrical energy and release it when needed.
Do you like ?187
Read more -
What are the daily maintenance of electric forklifts?
Electric forklifts are important equipment in warehousing...Do you like ?151
Read more -
"Electric Forklift Maintenance: Longer Life and More Efficiency"
In view of the fact that many friends are still confused about the maintenance of electric forklifts, Xiaobian specially summarized the maintenance knowledge of electric forklifts<...
-
"Level 3 maintenance is indispensable! Forklift maintenance strategy"
Do you like ?133
Read more
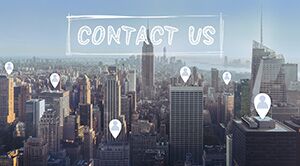